“Prefabricated houses” is a term in the construction industry referring to small, affordable houses with components completed in a factory. So how many types of prefabricated houses are there, and what are their pros and cons? All will be covered in today’s article by Việt Sơn.
What is a prefabricated house?
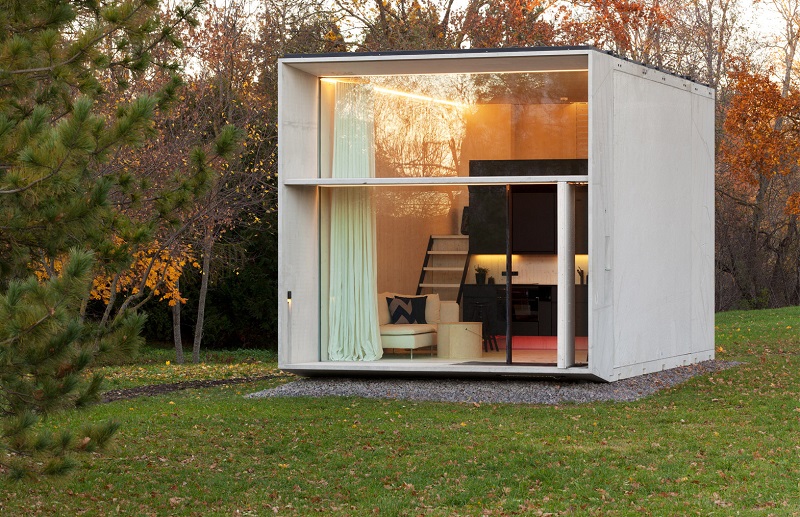
A prefabricated house, also known as a modular house, is a type of house where the main components of the house are built outside the construction site in a factory, then delivered and assembled on site (in an area where construction is allowed and desired by the owner). Historically, prefabricated houses were known as temporary housing with low quality during World War II in the UK. However, over time, prefabricated houses have been improved and developed to meet the cost-effective needs of users, so both quality and style are highly evaluated.
In addition, “prefabricated” means “pre-manufactured,” somewhat reflecting the negative aspects of this type of housing. As a result, when modernized, people have shifted to calling it “modular homes” – referring to a more advanced, cost-effective and convenient form.
In addition, the term “prefab” means “previously fabricated,” which reflects some negative connotations associated with this type of house. As a result, as it became more modern, the term “modular” or “prefabricated” became more commonly used to refer to this innovative, cost-effective, and highly convenient form of housing.
Types of Prefabricated Houses
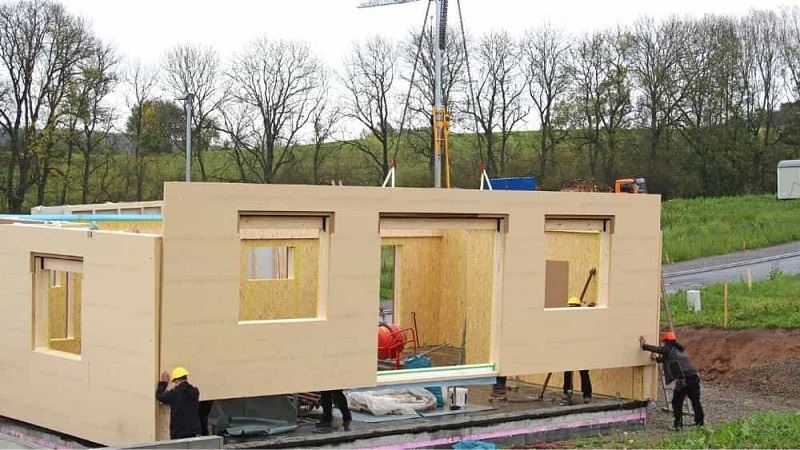
Current classifications of prefab houses vary depending on the location, purpose, and style. Typically, in Vietnam, they are divided into four main groups:
Residential Prefab Houses: primarily used for living, household, or rental purposes. The size of the house is relatively small to medium, with a scientific and functional interior layout, capable of accommodating many items, and demanding high aesthetic values.
Industrial Prefab Houses: used as storage warehouses or workshops. The scale of this type of house is quite large and can be assembled from multiple modules.
Commercial Prefab Houses: commonly used for small-scale convenience stores, supermarkets, or family grocery stores. The advantage of this type of house is that it provides spacious and cost-effective space for businesses.
Military Prefab Houses: suitable for short-term military housing, prefab houses are a convenient and cost-effective alternative to traditional housing, allowing the military to move to different areas more easily.
Advantages of Prefabricated Houses
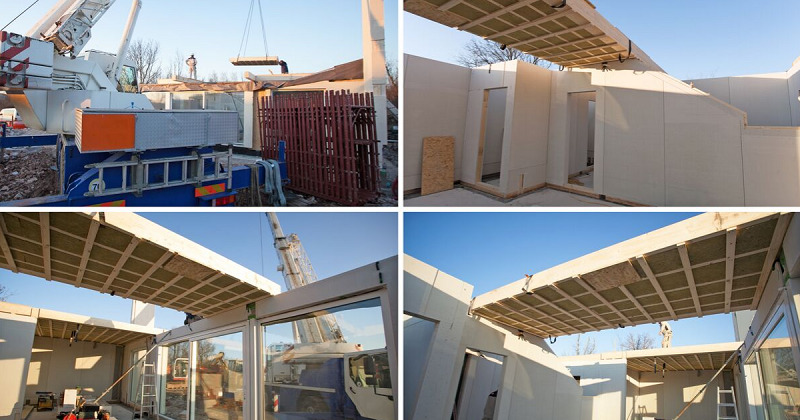
When considering buying a prefab house, it is important to weigh its advantages and disadvantages to determine if it suits your needs and budget.
Cost savings
One of the favorite features of prefabricated houses is that they are cheaper by 20% – 30% compared to traditional houses. The cost of prefabricated houses mostly depends on the size of the house, the larger the house, the higher the cost and vice versa, smaller or medium-sized houses will have more affordable prices.
Fast construction time
It takes about 7 months to 1 year to complete a traditional house, but with prefabricated houses, it only takes 2-3 months after choosing the desired style and owning the land documents. The construction time of prefabricated houses is shorter than half of traditional houses, not to mention it will be even faster if the weather is favorable and there are plenty of laborers.
Energy efficiency
Convenience is one of the initial purposes of creating prefabricated houses, so it is not surprising that modern prefabricated houses always integrate solar energy panels and rainwater collection systems to meet the living needs of homeowners. In addition, prefabricated houses are often built in open spaces – receiving natural light and wind as much as possible to minimize the use of electricity, thereby not only saving costs for homeowners but also contributing to environmental protection.
Disadvantages of prefabricated houses
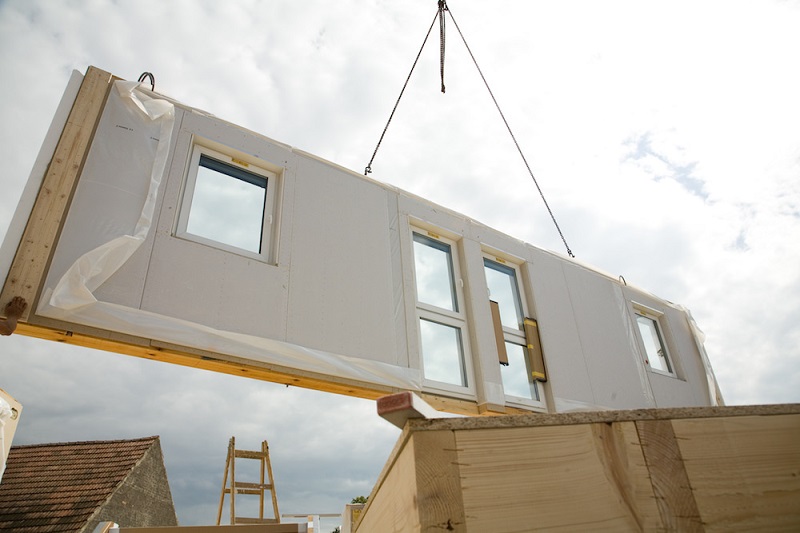
Difficult transportation
Because prefabricated houses are produced in factories, there will be a cost for transportation to the final assembly location. In other words, transportation costs are higher when the size of the house is larger and the distance from the production location to the final assembly location is farther away. Not to mention, you will incur a significant loss if the accessories are damaged during transportation.
Asset costs
There will be some additional fees if you buy a house such as taxes, paperwork completion costs… At the same time, you also have to spend a large amount of money to buy land if it is not already available.
Resale value
Although it is a trendy house type, the resale value of prefabricated houses is not high and easily squeezed in price. Therefore, to maintain the highest possible house value, you should renovate and take care of the house regularly.
Price of prefabricated houses
Not only raw materials, the price of prefabricated houses also relates to other factors such as labor costs, complexity… Among them, the most important is the area of the house, because according to the current calculation method, the price of prefabricated houses will be calculated based on m2. In other words, you should have the desired house area in mind before consulting the price. Besides, the recent price of 1m2 of houses ranges from 1.5 – 4 million, depending on whether the materials you choose are good or not.
You can estimate the cost by multiplying the price range with the desired square footage for owning a prefabricated house. Here are some beautiful designs for your reference:
20+ Prefabricated house models
If you have a love for or a need to buy a prefabricated house, here are some beautiful designs for your reference:
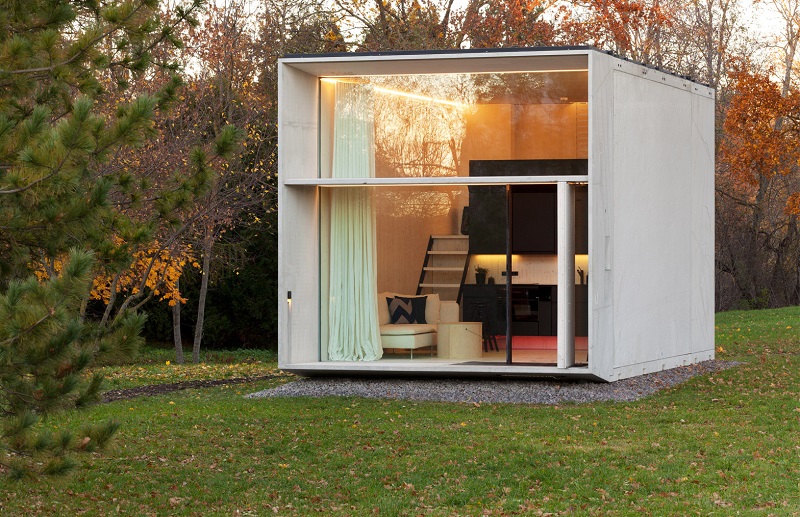
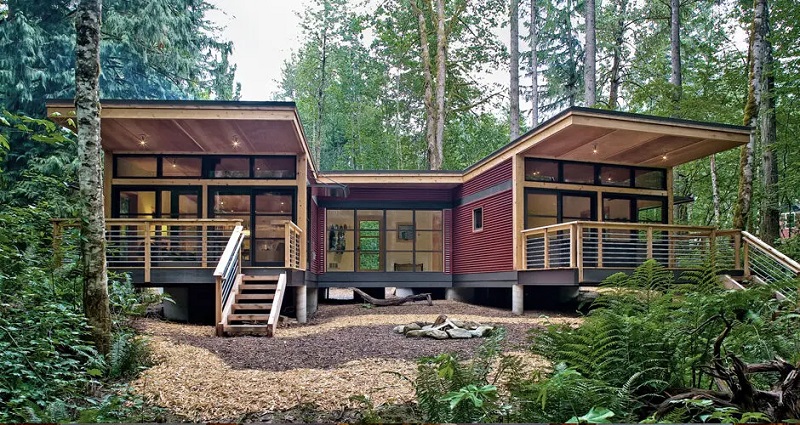
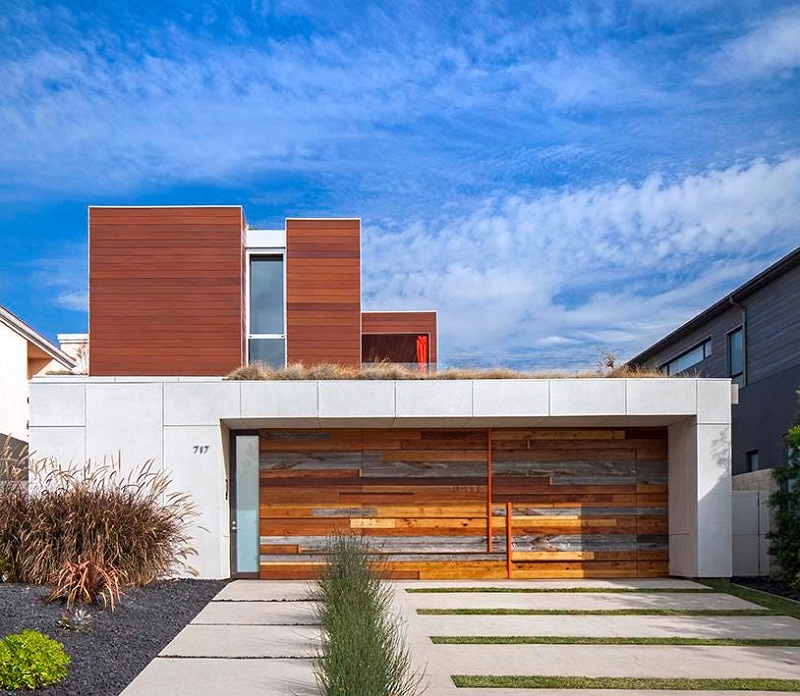
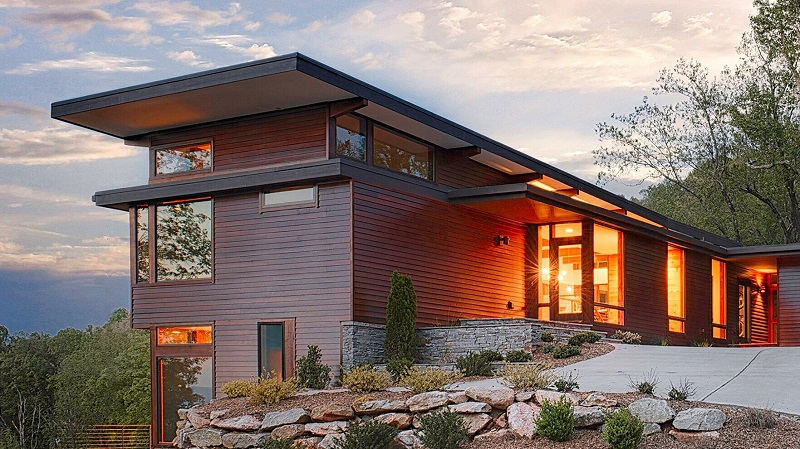
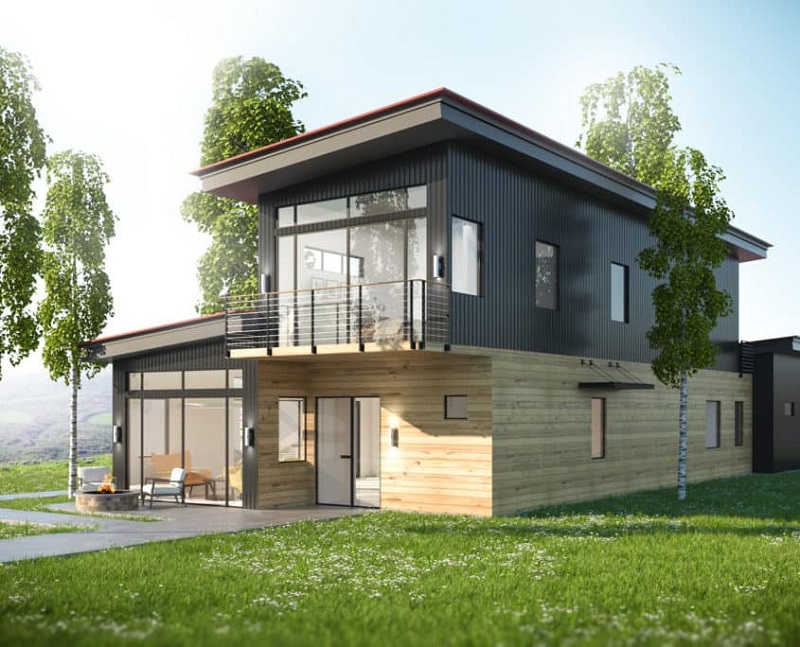
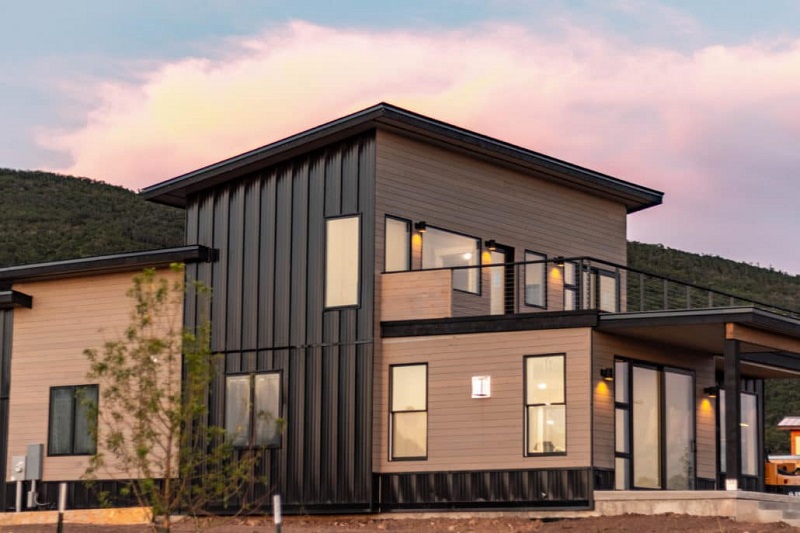
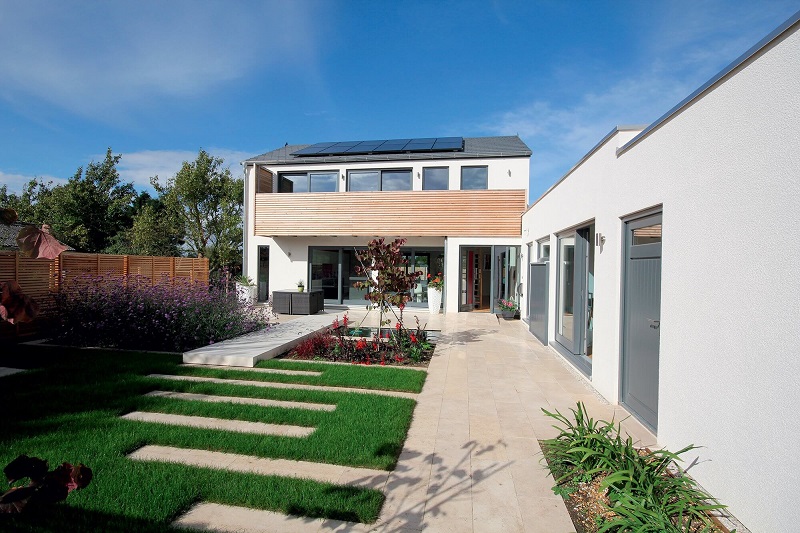
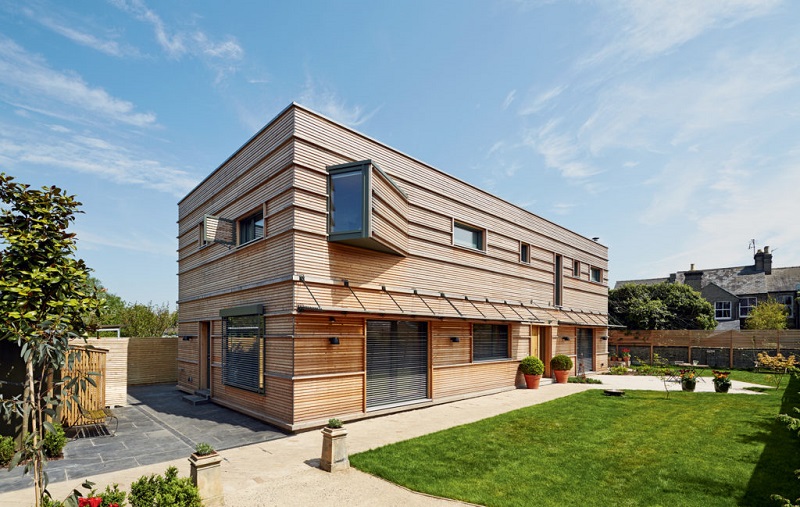
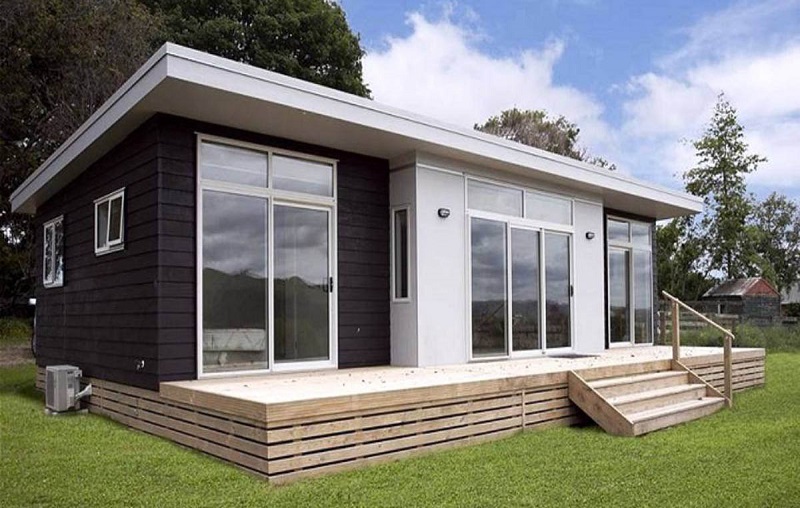
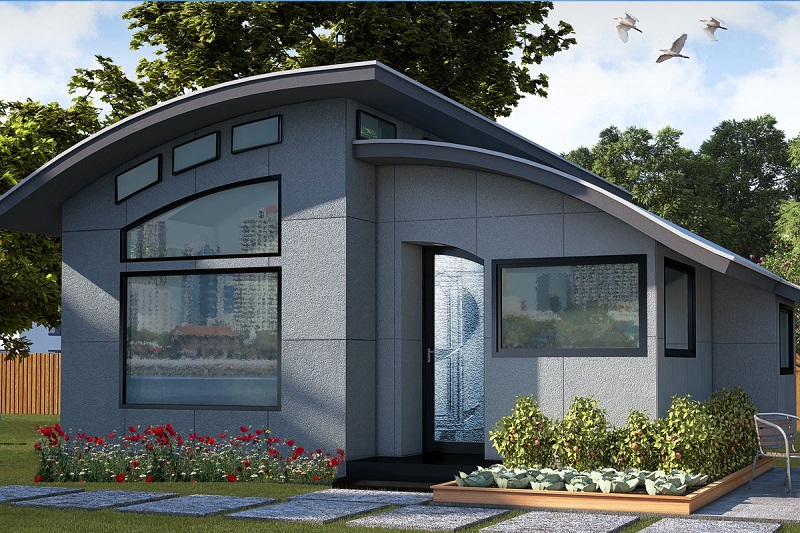
Prefabricated houses are a top choice in many European countries for those with limited finances or who frequently move. However, this style is still relatively new in Vietnam. Therefore, if you want to own a prefabricated house, it is advisable to do more research or seek advice from experienced individuals before starting.