CNC Turning
CNC turning is considered an effective method in metal cutting, commonly used in the field of mechanical processing. The products of this method are mainly round and rotating such as smooth shafts, threads, holes, stepped shafts, etc. There are many types of lathes with different sizes, so the products are also highly diverse.
In today’s technological age, CNC turning is thriving due to its high precision and superior speed compared to traditional methods. As a result, CNC turning is widely applied in various fields such as automotive parts manufacturing, machinery, watches, computers, and more.
What is CNC Turning?
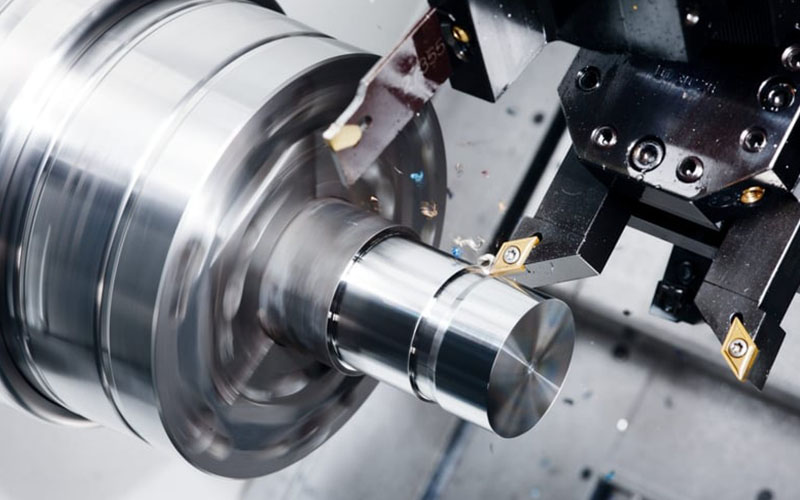
CNC turning (Computer Numerical Control) is a modern machining method that uses automated numerical control machines to turn and machine parts with high precision and speed. This method combines the movement of the workpiece and the tool to create products with the desired shapes. The processes are automatically controlled by programmed commands on a computer.
CNC turning is quite similar to the CNC milling process. However, unlike CNC milling, where the workpiece is held stationary while the cutting tool rotates, in CNC turning, the cutting tool is held stationary while the workpiece rotates.
CNC turning is a manufacturing process that produces parts by “turning material” with a fixed cutting tool to form the desired shape.
Why Use CNC Turning?
CNC turning is ideal for creating cylindrical shapes or parts that are symmetric around their axis, such as chess pieces, bolts, studs, bearings, and washers. CNC turning also addresses some manufacturing challenges associated with CNC milling. For example, it allows you to easily create cuts under the cutting groove, while CNC milling machines require specialized cutting tools to achieve this.
CNC lathes also enable cutting operations along 3, 4, or 5 axes, allowing you to perform taper turning, grooving, threading, and parting, among other operations. This subtractive manufacturing process is particularly suitable for rapid prototyping and low-volume production.
Applications of CNC Turning
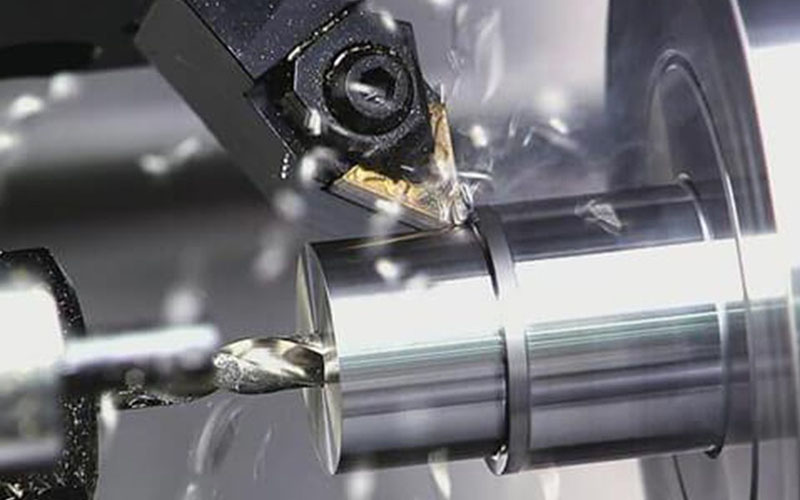
External Diameter Turning: Turning is an essential machining process in any mechanical manufacturing plant. The CNC turning method has many superior advantages over traditional universal lathes:
- Machining Complex Profiles: CNC turning can handle complex and difficult profiles that a conventional universal lathe cannot.
- High Economic Efficiency: Provides high economic efficiency and produces high-quality products.
CNC Grooving Turning: CNC turning is highly effective in cutting metals with chips. The methods allow users to perform by moving the workpiece and the turning tool. The main operating principle is the effective rotational movement of the workpiece, creating the cutting motion. This is a combination of longitudinal and transverse tool movements.
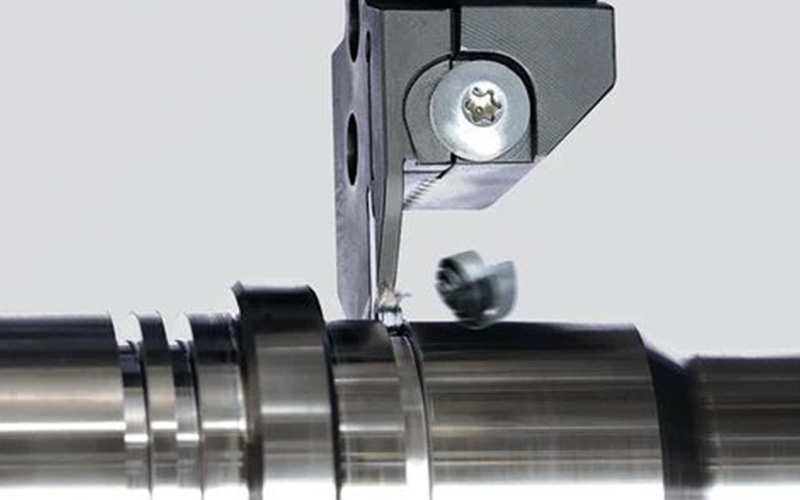
Advantages of CNC Turning
- High Precision: CNC turning achieves accuracy down to microns, producing intricate details.
- Fast Machining Speed: CNC turning can machine parts at high speeds, saving time and costs.
- High Flexibility: It can process complex parts that traditional lathes cannot handle.
- High Automation: CNC machines are controlled by computers, minimizing human intervention and increasing accuracy.
- Cost Savings: Automation and high speed help reduce production costs and increase efficiency.
CNC Turning Methods
- External Diameter Turning: Machining cylindrical parts by cutting away the outer material.
- Boring: Machining round holes, oval holes, or other shapes on flat surfaces.
- Facing: Creating smooth and polished surfaces on parts.
- Threading: Machining threads on part surfaces to create screw connections.
- Cutting Off: Using a turning tool to remove material and create grooves.
- Grooving: Creating grooves on the product shaft.
- Form Turning: Using turning tools to create complex shapes and high accuracy on part surfaces.
CNC Turning Process
- Study the Machining Technology: Read the drawings, select the workpiece, machine, and setup method, and determine the technological process.
- Design the Cutting Path: Use CAD/CAM software to create the tool cutting path.
- Program the Control System: Use manual or automatic programming to control the CNC machine.
- Check the Control Program: Ensure that the program operates accurately.
- Adjust the CNC Machine: Calibrate parameters and settings to ensure precision.
- Machine the Parts: Prepare the workpiece, cutting tools, and fixtures; start the control system and perform machining.
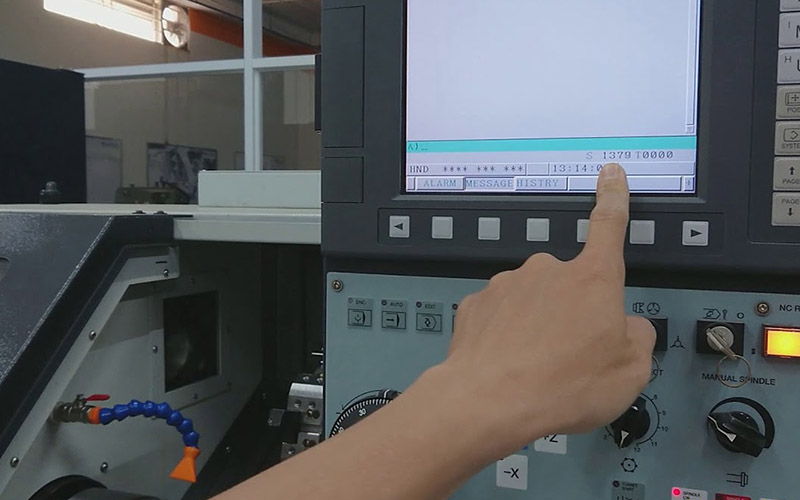
Viet Son Precision CNC Turning Services
CNC turning is considered an effective method in metal cutting, widely used in the machining industry. The products of this method are mainly rotating shapes such as smooth shafts, threads, holes, and stepped shafts. There are many types of lathes of different sizes, so the products are also highly diverse.
At Viet Son, we provide turning services with various methods to meet the maximum needs of customers. Thanks to our modern software and machinery, our precision mechanical products always ensure quality, fast machining times, and the best prices.
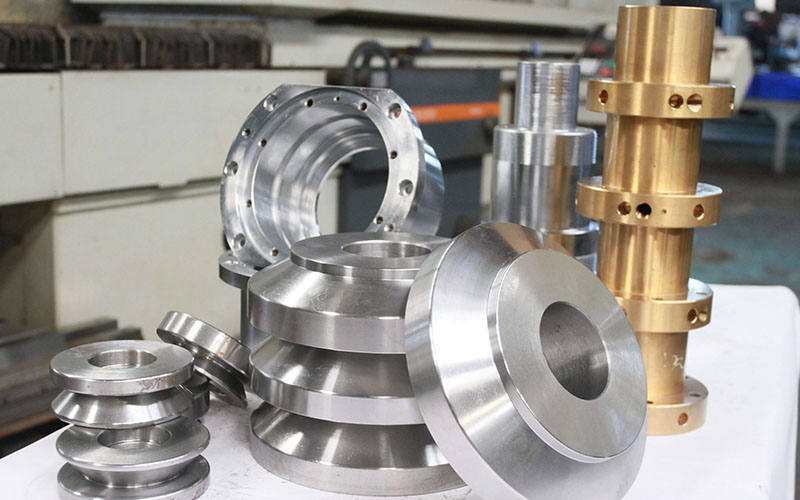
Why Choose Viet Son’s CNC Turning Services?
Viet Son has many years of experience in CNC design and turning in Vietnam.
- Viet Son has been a partner of many domestic enterprises and foreign partners.
- Our products are always machined according to standardized processes to simplify design, facilitate operation, and ensure accuracy throughout the process.
- Professional Service
- On-time Delivery
Contact Viet Son for detailed CNC turning consultation:
- Contact for Machining: 0922 668 868 (Zalo – Viber – WhatsApp)
- Address: Lot C2-7, Road N7, Tan Phu Trung Industrial Park, Tan Phu Trung Commune, Cu Chi District, Ho Chi Minh City
- Website: https://vietson.com.vn/
- Email: [email protected]
- Facebook: https://www.facebook.com/cokhivietson
- Youtube: https://www.youtube.com/channel/UC_n7V8NDRtO75pSOUOMiQ8w