In the field of modern mechanical machining, CNC turning has become the optimal solution to meet the demands for precision and efficiency. Viet Son Mechanical proudly stands as a leading provider of high-quality CNC turning services, assisting customers in completing complex mechanical components with outstanding durability and uniformity.
I. Introduction to CNC Turning Machining
What is CNC Turning Machining?
CNC turning is a machining process that uses a CNC lathe (Computer Numerical Control) to create mechanical parts with precise shapes and dimensions according to specifications. In this process, the raw material is fixed and rotated on the lathe, while cutting tools advance into the material to shape the product following pre-programmed cutting paths. This method is commonly used to produce components such as shafts, gears, and other parts with round or symmetrical surfaces.
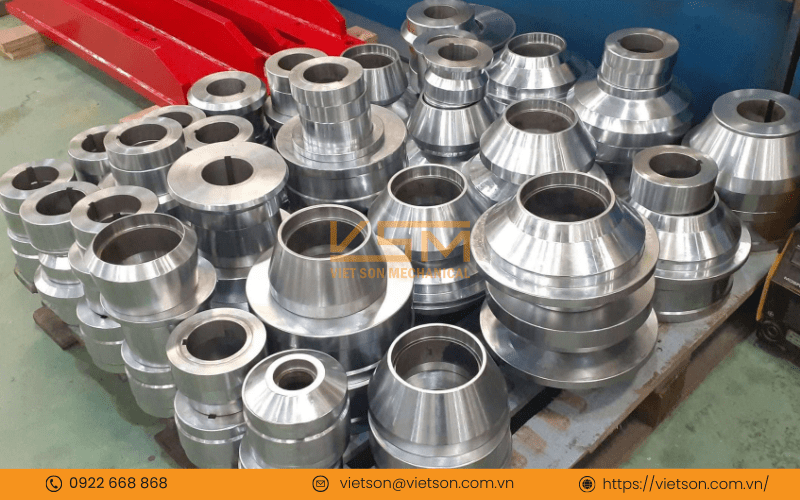
Main Features of CNC Turning Machining
- Operating Principle: The lathe performs cutting by moving the cutting tool along the material’s surface, removing unwanted layers to create the desired shape.
- Materials Used: CNC turning can be applied to various materials, including metals (such as steel and aluminum), plastics, and wood.
- Precision: CNC turning can achieve high accuracy, with the capability to machine components with complex sizes and shapes.
- Applications: This method is widely used in machine manufacturing, automotive, aerospace, and many other industrial fields.
CNC turning is one of the fundamental and important methods in mechanical machining, playing a vital role in modern production processes.
II. Common CNC Turning Machining Methods
- Straight Turning (External Turning): This is the most common method used to machine the outer surfaces of cylindrical components like shafts and pipes, producing smooth and accurate surfaces along the length of the part.
- Bore Turning (Internal Turning): Bore turning is used to machine holes or smooth the inner surfaces of components, such as drilling holes in shafts or pipes.
- Conical Turning: This method is used for machining conical components, with a gradually decreasing or increasing diameter along the length of the part, such as tapered shafts or conical shapes.
- Thread Turning: Thread turning creates threads on the surface of components, used to manufacture bolts, nuts, or other threaded connections.
- Chamfering: This method is used to bevel the edges of components, removing sharp corners or smoothing edges before assembly, making it easier to fit parts together and preventing hazards during use.
- End Face Turning: This method is used to machine the end face of components, creating a flat surface perpendicular to the component’s axis, commonly applied in machining shafts or discs to ensure flat and smooth end faces.
Different CNC turning methods allow for the production of components with high precision and surface quality, suitable for various requirements and applications in the industry. The choice of the appropriate machining method depends on the shape, size, and material of the component to be machined.
Reliable CNC Turning Machining Service Provider: Viet Son Mechanical
Viet Son Mechanical Engineering is a reputable provider of CNC turning services with many years of experience, modern equipment, and a professional process. Our skilled technicians ensure the delivery of high-precision products that meet stringent technical requirements. Trusted by numerous domestic and international enterprises, Viet Son is a reliable partner in the mechanical industry.
Contact for machining: 0922 668 868 (Zalo – Viber – WhatsApp)
Website: https://vietson.com.vn/
Email: [email protected]
III. Applications of CNC Turning Machining
CNC turning has many important applications in manufacturing and production.
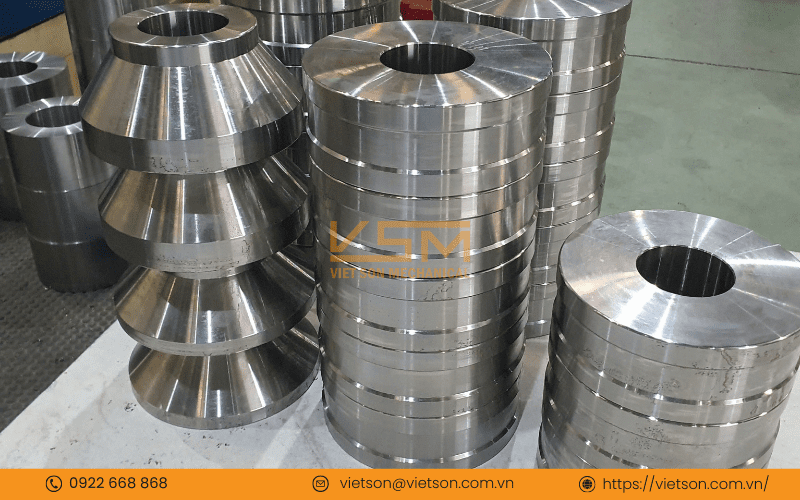
- Creating Accurate Parts: CNC turning allows for the production of parts with circular, conical, and other complex shapes with high precision, which is crucial for applications that demand dimensional and shape accuracy.
- Surface Machining: This method improves the surface quality of parts, reducing roughness and creating a smooth finish. This is essential in applications where a smooth surface is a key requirement, such as in automotive and aerospace industries.
- Production of Threaded Components: Thread turning is a vital application of CNC turning, allowing the creation of threads on component surfaces. These parts are commonly used in machinery, piping, and connections.
- Machining Complex Components: CNC turning can produce complex shapes and structures that are difficult to achieve with other machining methods, helping to manufacture parts with high technical requirements.
- Machining Symmetrical Parts: This method is highly effective for machining symmetrical components, such as shafts, gears, and other rotating parts, ensuring consistency and accuracy in production.
- Minimizing Material Waste: CNC turning can minimize material waste during production by precisely removing unwanted layers to create the desired shape.
- Enhancing Operational Performance: Parts machined using turning methods generally exhibit higher durability and stable performance due to precise machining and effective cutting.
- Automation Capability: With advancements in CNC technology, CNC turning can be automated, enhancing productivity, reducing production costs, and improving consistency in the machining process.
The CNC turning method not only produces mechanical components with high precision but also provides numerous benefits in performance and quality. Its flexibility in application and automation capability has made CNC turning an indispensable part of modern production processes.
IV. CNC Turning Machining Process
The CNC turning process includes specific steps from preparation to product completion.
- Preparation and Design:
- CAD Drawing Design: Use CAD software to design parts with technical specifications for dimensions, accuracy, and surface requirements.
- CNC Code Programming (G-code): Convert the drawing into CNC code to control the lathe in performing machining steps along a defined path.
- Preparation of Raw Material and Cutting Tools:
- Select Workpiece: Choose a workpiece with suitable material and size for the part to be machined.
- Select Appropriate Cutting Tool: Choose the appropriate type of tool, such as cylindrical turning tool, thread turning tool, or conical turning tool, according to the requirements.
- Check Cutting Tools and Workpiece: Ensure tools are sharp and the workpiece is securely clamped.
- Setting Up the CNC Machine:
- Secure Workpiece: The workpiece is firmly clamped on the spindle chuck to ensure no shaking during machining.
- Input CNC Code into the Machine: The programmed G-code is loaded into the CNC lathe.
- Set Machining Parameters: Establish parameters like spindle speed, feed rate, and cutting depth according to the material type and product requirements.
- Testing and Program Verification:
- Run Simulation: Perform a toolpath simulation on the machine to detect potential errors.
- Run Idle Test: Conduct a dry run at low speed without a workpiece to verify the accuracy of the code.
- Commencing Machining:
- Official Machining: The machine automatically performs cutting, turning, and shaping the product according to the programmed path.
- Monitor the Machining Process: The operator monitors the process to detect and resolve issues if they occur (e.g., tool wear, vibration).
- Checking and Finishing the Part:
- Measure Dimensions and Quality Check: After machining, check dimensions, accuracy, and surface quality of the product.
- Surface Treatment: If necessary, perform surface treatment steps like grinding or polishing to enhance aesthetics and durability.
- Cleaning and Maintenance of the Machine:
- Remove Workpiece: Detach the machined part from the chuck.
- Clean and Maintain the Machine: Clean the cutting tools, chucks, and perform maintenance to prepare for the next production cycle.
This process helps CNC machining units, such as Viet Son Mechanical , produce high-quality products, ensuring accuracy and consistency for mechanical components that meet the stringent requirements of industrial sectors.
At Viet Son, our products are always CNC turned according to a standardized process to simplify design, facilitate operator convenience while ensuring precision throughout the working process. Contact Viet Son for detailed CNC turning consultation:
Contact for machining: 0922 668 868 (Zalo – Viber – WhatsApp)
Website: https://vietson.com.vn/
Email: [email protected]
V. Advantages of CNC Turning Machining
CNC turning is one of the most popular and important machining methods, widely applied in manufacturing. With the ability to create precise and high-quality parts, CNC turning not only meets strict technical requirements but also brings many benefits to the production process.
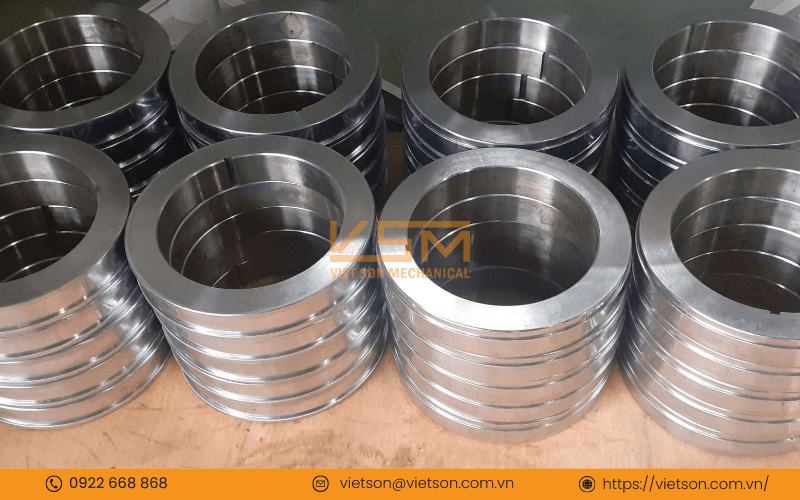
- High Precision: CNC turning allows for producing components with high dimensional and shape accuracy, meeting stringent technical requirements.
- Good Surface Finish: The CNC turning process improves the surface quality of the product, reducing roughness and creating a smooth finish.
- Diversity in Application: CNC turning can be used for various materials, including metals, plastics, and wood, as well as for many different component shapes.
- Capability to Machine Complex Parts: CNC turning can produce components with complex shapes, including contoured and threaded surfaces.
- Increased Productivity: Modern CNC lathes can automate the machining process, enhancing productivity and minimizing production time.
- Reduced Material Waste: The turning process can accurately remove unwanted material, helping to save raw material costs.
- Easy Maintenance and Operation: Traditional and CNC lathes are often designed to be user-friendly, reducing training time for operators.
- Flexibility: Lathes can be adjusted to machine various components, from single products to mass production.
- Time Efficiency: The CNC turning process is generally quick and efficient, shortening production time.
CNC turning offers many outstanding advantages, from high precision and good surface finish to flexibility in application, making it an essential method in the mechanical manufacturing industry.
Contact Viet Son for detailed CNC turning consultation:
Contact for machining: 0922 668 868 (Zalo – Viber – WhatsApp)
Website: https://vietson.com.vn/
Email: [email protected]
VI. Applications of CNC Turning Machining in Industry
CNC Turning Machining is widely applied in many industrial fields due to its flexibility and ability to create precise parts.
- Machinery Manufacturing: Machining machine parts such as shafts, gears, and other mechanical components. These parts require high precision to ensure the machine’s performance.
- Automotive Industry: Manufacturing components such as crankshafts, camshafts, and other engine parts. CNC turning machining helps produce parts with high precision and durability, ensuring the vehicle’s efficient operation.
- Aerospace Industry: Machining complex and lightweight parts for aircraft, such as airframes, engine components, and landing gear. Precision in machining is crucial to ensure safety in the aerospace industry.
- Electronics Industry: Manufacturing small parts for electronic devices such as casings, connectors, and other components. CNC turning machining helps create parts with high precision and excellent surface finish.
- Medical Equipment Manufacturing: Machining parts for medical devices such as ultrasound machines, X-ray machines, and surgical instruments. The quality and precision requirements in the medical field are very high.
- Food Processing Industry: Manufacturing parts for food processing machinery, such as shafts, gears, and other components. CNC turning machining ensures that equipment operates efficiently and safely in the food processing industry.
- Energy Industry: Machining parts for generators, wind turbines, and equipment in the energy sector. The precision and durability of these components are critical to ensure performance and safety.
CNC turning machining plays a vital role in various industrial fields, from machinery manufacturing to aerospace and healthcare. With the ability to produce precise and durable parts, CNC turning machining not only enhances production efficiency but also ensures the quality of the final product.
At Viet Son Mechanical , thanks to modern equipment and advanced software, the precision mechanical products we provide always ensure superior quality, quick machining time, and the most reasonable cost.
Contact Viet Son Mechanical for detailed CNC turning machining consultation:
- CNC machining contact: 0922 668 868 (Zalo – Viber – WhatsApp)
- Website: https://vietson.com.vn/
- Email: [email protected]
VII. Factors Affecting the Quality of CNC Turning Machining
In the CNC turning machining process, ensuring product quality is the top priority that manufacturers need to focus on. The quality of machining not only affects the product’s performance but also determines customer satisfaction. To achieve the best quality, many factors need to be considered and controlled throughout the machining process.
- Machining Materials: The material properties such as hardness, ductility, and wear resistance affect the cutting ability and durability of the machined part. Different materials require different machining methods and cutting tools.
- Cutting Tools: The type, sharpness, and shape of the cutting tool affect the surface quality and accuracy of the product. Worn or unsuitable cutting tools can lead to errors and subpar surfaces.
- Machine Parameters: The spindle speed, feed rate, and other machine parameters must be set accurately. These parameters directly impact the cutting process and product quality.
- Machining Process: The machining process must be carefully planned, including cutting methods, operation sequences, and quality inspection steps. An illogical process can lead to product defects.
- Operator Skills: The training and experience of the machine operator significantly influence machining quality. Experienced operators will know how to adjust the machine and handle issues that arise during the machining process.
- Machinery and Equipment: The quality and accuracy of the lathe also affect the machining results. Modern machinery with advanced technology typically yields better results than older or lower-quality machines.
VIII. Viet Son Mechanical – Professional and Reputable CNC Turning Machining
Viet Son Mechanical is proud to be a leading unit with many years of experience in the design and CNC turning machining field in Vietnam. With trust from many domestic enterprises and international partners, Viet Son Mechanical has affirmed its position in the market.
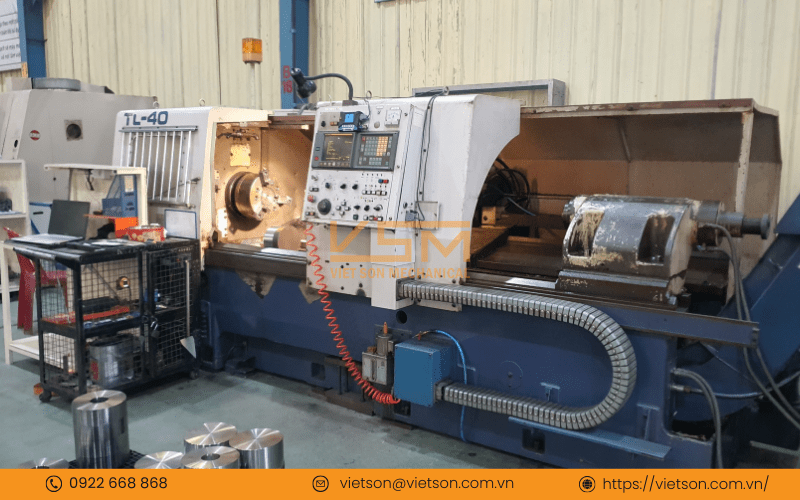
CNC TURNING MACHINING
The products of Viet Son Mechanical are manufactured according to a strict standardized process to optimize design and create maximum convenience for operators. At the same time, we commit to maintaining superior accuracy and quality throughout the machining process, providing the best solutions for customers.
Contact Viet Son Mechanical for detailed CNC turning machining consultation:
- CNC machining contact: 0922 668 868 (Zalo – Viber – WhatsApp)
- Address: Lot C2-7, N7 Street, Tân Phú Trung Industrial Zone, Tân Phú Trung Commune, Củ Chi District, Ho Chi Minh City
- Website: https://vietson.com.vn/
- Email: [email protected]
- Facebook: https://www.facebook.com/cokhivietson
- YouTube: https://www.youtube.com/channel/UC_n7V8NDRtO75pSOUOMiQ8w