CNC gear machining has brought significant advancements to the mechanical engineering industry, especially in the production of high-precision gear components. At Viet Son, we take pride in being a leading provider of high-quality CNC gear machining services, utilizing modern technology and advanced machinery.
I. General Introduction
Definition of CNC Gear Machining
CNC gear machining is the process of using CNC (Computer Numerical Control) machines to manufacture gears with high precision. In this process, the gear designs are pre-programmed, and the machine automatically performs cutting, milling, turning, or grinding to create the final product.
This process offers several benefits, including:
– High precision: Minimizes errors during the machining process.
– Automation: Reduces human intervention, saving time and effort.
– Flexibility: Can produce various types of gears with diverse designs.
CNC gear machining is commonly applied in industries such as automotive, machinery manufacturing, aviation, and electronics, where precision and performance are critical.
CNC Gear Machining at Viet Son Mechanical Company
At Viet Son, we specialize in providing CNC gear machining services using modern technology and a team of skilled engineers. We are committed to delivering high-quality products that meet all the technical requirements and strict standards of our clients.
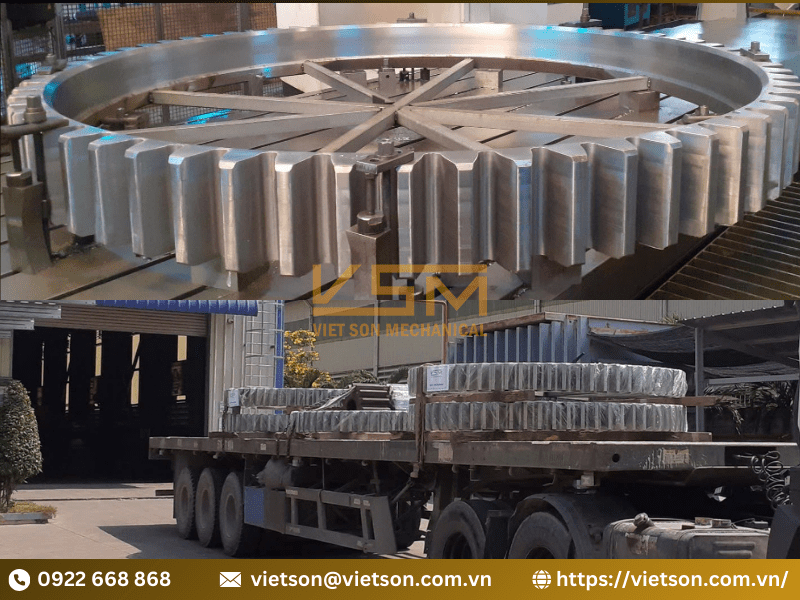
With a strict quality control process, Viet Son ensures that each gear product achieves optimal precision and durability. Let us help you optimize your production process and enhance your business efficiency.
Contact for machining:
Phone: 0922 668 868
Website: https://vietson.com.vn/
Email: [email protected]
II. Common Types of CNC Gears
CNC gears play an essential role in many industrial applications. Below are the most common types of CNC gears, helping you better understand their diversity and applications:
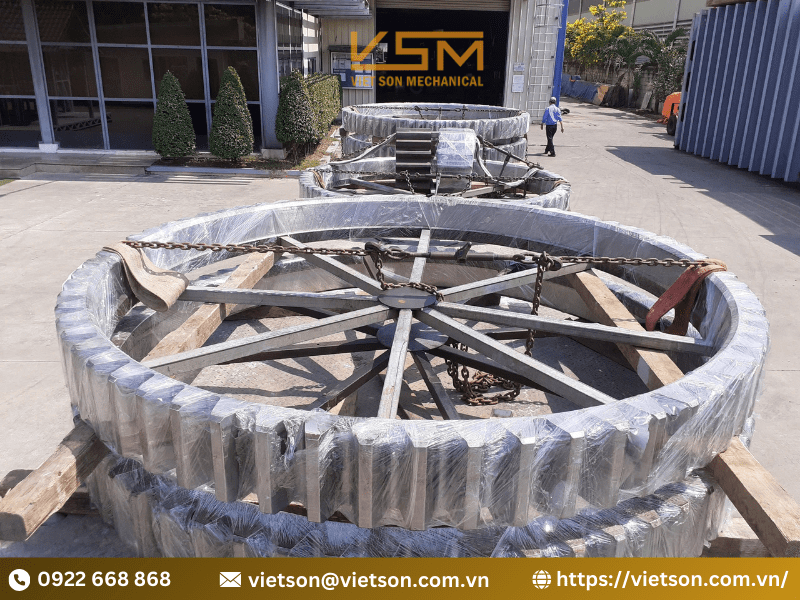
- Cylindrical Gear: Cylindrical gears have a round shape and are widely used in linear drive systems. They help efficiently transmit force between parallel shafts.
- Bevel Gear: With a conical shape, bevel gears transmit motion between shafts positioned at an angle to each other. Commonly found in automotive gearboxes and machinery.
- Helical Gear: Helical gears have angled teeth, which help reduce noise and increase transmission capacity. They are often used in applications requiring smooth operation.
- Worm Gear: Using a worm to drive another gear, worm gears are typically used in high-ratio transmission systems.
- Planetary Gear: Consisting of a central gear and multiple surrounding gears, planetary gears are often used in complex transmission systems, such as automatic gearboxes.
- Special Gear: These are custom-designed gears tailored for specific applications, including those with special shapes or structures.
The variety of CNC gears not only reflects their diverse shapes but also their suitability for many industrial applications. Selecting the right type of gear will enhance the efficiency and durability of machinery systems. If you need more information or consultation on CNC gears, please contact Viet Son Mechanical Company for detailed support.
Contact for CNC gear machining at Viet Son:
Phone: 0922 668 868
Website: https://vietson.com.vn/
Email: [email protected]
III. CNC Gear Machining Process
The CNC gear machining process includes several steps from design to production:
Design and Programming:
- CAD Design: The first step is creating a 3D drawing of the gear using design software such as AutoCAD or SolidWorks.
- CNC Programming: Based on the drawing, the programmer writes G-code to control the CNC machine to perform the necessary operations.
Material Preparation:
- Select the appropriate material for the gear, typically steel, aluminum, or special alloys.
- Cut the material into rough sizes, suitable for the gear’s dimensions.
Machining Process:
- Cutting and Milling: Use a CNC milling machine to cut and shape the gear teeth according to the design.
- Turning: If necessary, use a lathe to finalize the gear’s shape and dimensions.
- Grinding: For gears requiring high precision, grinding is performed to achieve a smooth surface and optimal accuracy.
Quality Control:
After machining, the product is inspected with precise measurement equipment to ensure it meets technical standards. Inspections include checking concentricity, dimensions, and surface smoothness.
Finishing and Surface Treatment:
If required, gears undergo surface treatments such as plating, painting, or heat treatment to enhance durability and corrosion resistance.
Packaging and Delivery:
Finally, the finished gears are carefully packaged and delivered to the customer as requested.
The CNC gear machining process not only requires high technical skills but also precision at every step to ensure the final product meets the highest quality standards. At Viet Son, we are committed to carrying out this process professionally, delivering perfect gear products to our customers.
IV. Advantages of CNC Gear Machining
CNC gear machining offers many outstanding benefits compared to traditional machining methods:
- High Precision: CNC machines are programmed to perform operations with high accuracy, minimizing errors in the final product.
- Automated Process: CNC machining automates the production process, reducing human intervention, saving time, and minimizing the risk of human errors.
- Increased Productivity: CNC machines can operate continuously, 24/7, increasing production capacity without needing breaks like manual methods.
- Flexibility: CNC machines can produce various types of gears with different designs by simply changing the programming.
- Cost Savings: While the initial investment in CNC machines may be high, in the long term, reducing material waste, saving time, and increasing productivity will help reduce production costs.
- High Surface Quality: CNC machining allows for a smoother surface finish, reducing the need for additional surface treatment steps.
- Easy Quality Control: The CNC machining process is often integrated with automatic quality control systems, helping detect and correct errors early.
CNC gear machining not only delivers superior quality products but also optimizes the production process.
V. Applications of CNC Gears in Reality
Gears are a crucial component in mechanics, helping transmit motion and adjust force in many systems CNC gear machining (Computer Numerical Control) has significant applications in both industry and everyday life.
Industrial Applications
- Automotive Industry: Gears are used in gearboxes, engines, and steering systems. CNC gear machining ensures high precision and consistency, improving performance and reducing noise.
- Aviation Industry: Gears in aircraft engines and control systems must meet extremely high precision and durability standards. CNC machining helps meet the stringent safety and performance requirements of the aviation industry.
- Machinery Manufacturing: Gears are used in manufacturing machinery, machine tools, and industrial equipment. CNC machining helps produce gears with complex shapes and sizes, meeting various application needs.
- Energy Sector: Gears are used in wind turbines, generators, and transmission systems in renewable energy. Gear precision and durability are crucial for ensuring efficiency and reliability.
- Food Processing Industry: Gears are used in food processing machines to transmit motion and control the production process. Precision machining ensures safety and efficiency in production.
Practical application
- Consumer Devices: Small gears are used in watches, blenders, household appliances, and electronics. CNC machining creates gears with high precision, ensuring smooth operation.
- Toys: Many mechanical toys use gears to create motion. CNC machining allows the production of small and complex parts with high accuracy.
- Sports Equipment and Tools: Gears are used in many sports devices, from bicycles to treadmills, where durability and precision in movement are required.
- Models and Simulations: CNC gear machining is used in creating models or simulations for engineering projects, research, and product development.
CNC gear machining plays an important role in both industrial and everyday applications, from manufacturing complex parts in heavy industries to producing everyday consumer devices. The precision and customization capabilities of CNC technology enhance product quality and meet diverse market needs.
VI. Factors Affecting the Quality of CNC Gear Machining
There are many factors that affect the quality of CNC gear machining, from machine setup and adjustment to material selection and the technology used.
Gear Material
- Material selection: The quality of the material greatly influences the durability, wear resistance, and performance of the gear. Alloy steel with high hardness is suitable for heavy-duty applications, while plastic and aluminum alloys are ideal for light applications that require high precision.
- Material characteristics: Properties such as hardness, thermal conductivity, and corrosion resistance of the material will affect machining, especially the cutting speed and choice of cutting tools.
CNC Machine Accuracy
- Machine accuracy: CNC machines require high precision to cut and shape gears accurately. Any deviation in position or size can reduce the quality and cause operational errors.
- Machine maintenance: An important factor in maintaining accuracy is ensuring that CNC machines are always in good condition, regularly maintained to avoid mechanical faults or performance loss during machining.
Cutting Tools and Cutting Conditions
- Cutting tool quality: Gear cutting tools need to be selected based on the material type. Tools made from carbide or synthetic diamonds have high durability and cutting efficiency. If the tool is worn or not sharp enough, the product is likely to have defects or an unsatisfactory surface finish.
- Cutting speed and feed rate: Cutting speed, spindle speed, and feed rate must be adjusted to match the material and machining requirements. Improper speed can damage the cutting tool and affect the surface quality of the gear.
CNC Programming
- Design and programming: Accurate CNC programming is crucial for machines to perform the necessary operations to create gears with the desired size and shape. Programming errors can lead to dimensional and angular deviations.
- Support software: High-quality CAD/CAM software helps optimize the design process and simulate the cutting process before production, ensuring higher precision.
Machining Environment
- Temperature: Temperature during machining can affect product accuracy, especially when machining metal materials. Uneven heating can lead to deformation or surface damage to the gear.
- Coolant: Proper use of coolants helps reduce heat, improve surface finish, and extend the life of cutting tools. If not controlled, high temperatures will cause rapid tool wear and material deformation.
Quality Control
- Measurement and inspection: After machining, gears must be thoroughly inspected for dimensions, precision, and concentricity. 3D measuring machines and precision measurement equipment ensure the gears meet technical standards.
- Process stability: The machining process must be continuously monitored and adjusted to ensure consistent quality across production batches. If the process is unstable, gear quality can vary between products.
The quality of CNC gear machining is influenced by many factors, from material selection, CNC machine accuracy, cutting conditions, programming, machining environment to quality control. Optimizing each of these factors ensures high-quality gears that meet technical requirements and are applicable in various industries.
VII. Quality Standards in CNC Gear Machining
Quality standards in CNC gear machining are essential to ensure that the products meet technical requirements and performance expectations.
Dimensional Standards
- Tolerances: Dimensional accuracy must comply with specified technical parameters, ensuring the gear fits correctly with other components in the system.
- Dimension inspection: Use measuring devices such as calipers, micrometers, or 3D measurement machines to verify the critical dimensions of the gear.
Shape and Structural Standards
- Gear tooth shape: Gear teeth must have the exact shape according to the design, including depth, width, and cross-sectional profile.
- Concentricity: Ensure gears are mounted concentrically to reduce friction and wear during operation.
Surface Standards
- Surface roughness: The gear surface must achieve a specific roughness level to ensure performance and longevity. Standards such as Ra (surface roughness) are often used for measurement.
- Surface inspection: Use surface roughness measuring equipment to check the specified surface requirements.
Material Standards
- Material: Gears must be made from materials that meet hardness, wear resistance, and durability requirements.
- Material inspection: Perform tests such as hardness checks, chemical composition analysis to ensure the material meets the standards.
Performance Standards
- Load capacity: Gears must withstand the load and pressure during operation without failure.
- Performance testing: Conduct load tests to verify the gear’s operational capability and lifespan.
Safety Standards
- Operational safety: Gears must meet safety standards to ensure no risks during use.
- Certification: International or regional safety standards such as ISO, ASTM, or industry-specific standards must be applied.
Quality Control Standards
- Quality control process: Inspection and evaluation procedures must be carried out throughout the production process to detect and address defects promptly.
- Inspection records: Record inspection results and certifications to ensure product traceability and transparency.
Quality standards in CNC gear machining form the foundation for ensuring the product meets technical, performance, and safety requirements. Adhering to these standards not only enhances product quality but also minimizes operational risks.
VIII. Viet Son Mechanical Engineering – Leading CNC Gear Machining Service
Viet Son is one of the leading companies in mechanical processing for the supporting industry in Vietnam and exports to many countries worldwide.
By integrating advanced technology and creativity into the production process, we not only manufacture mechanical products that meet international standards but also shape the trends in the industry.
Viet Son is a trusted and professional address in CNC gear machining in Ho Chi Minh City. We are always ready to listen and provide the best services and products to meet all customer needs.
Contact for machining: +84 922 668 868 (Zalo – Viber – WhatsApp)
Address: Lot C2-7, N7 Street, Tan Phu Trung Industrial Park, Tan Phu Trung Commune, Cu Chi District, HCMC
Website: https://vietson.com.vn/
Email: [email protected]
Facebook: https://www.facebook.com/cokhivietson
YouTube: https://www.youtube.com/channel/UC_n7V8NDRtO75pSOUOMiQ8w