CNC milling is one of the most modern and precise manufacturing techniques today. With CNC milling technology, we can produce mechanical parts with high accuracy, durability, and meet stringent requirements for dimensions and shapes. In this article, let’s explore in detail CNC milling and its applications in life with Viet Son Mechanical!
What is CNC Milling?
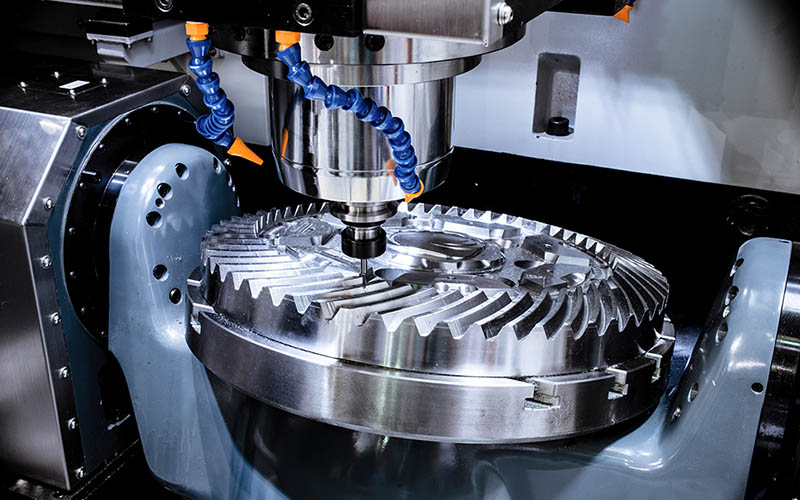
CNC stands for “Computer Numerical Control” which means computer-controlled numerical machining. CNC milling is a method of cutting material using a CNC milling machine.
CNC milling is a form of manufacturing that involves removing material to create a finished shape. The CNC process begins with creating a 3D CAD model of your desired part’s geometry before converting it into a computer program (G-code) using CAM software. This computer program then automates the cutting tool’s operation to produce your desired parts.
Types of CNC Milling Movements:
- Cutting Motion (Primary): The process of moving the tool around its axis.
- Feed Motion: The translational movement along the X, Y, and Z axes, which can be independent or combined.
The CNC milling method has numerous applications in medical device manufacturing, automotive, aerospace, and precision mechanical industries.
Advantages and Disadvantages of CNC Milling

Advantages of CNC Milling:
- High Precision: CNC milling can achieve very high accuracy, typically ranging from 0.005 to 0.01mm. This ensures that the machined parts have high precision and durability, and helps avoid rework due to errors during production.
- Flexibility: CNC machines can easily machine parts with complex sizes and shapes and can quickly switch between different jobs.
- Time-Saving: CNC milling can produce parts faster and more efficiently than traditional manufacturing methods, saving time and increasing productivity.
- Automation: CNC machines operate automatically, eliminating the need for a large workforce and minimizing human errors.
Disadvantages of CNC Milling:
- High Cost: CNC milling equipment is more expensive than traditional manufacturing equipment, increasing initial costs and requiring a significant investment.
- Requires High Skill: Operating CNC machines requires specialized skills and training. Therefore, production staff must have high technical expertise, increasing training costs.
- Difficulty in Repair: If a CNC machine breaks down, repairs can be complex, time-consuming, and costly
CNC Milling Methods
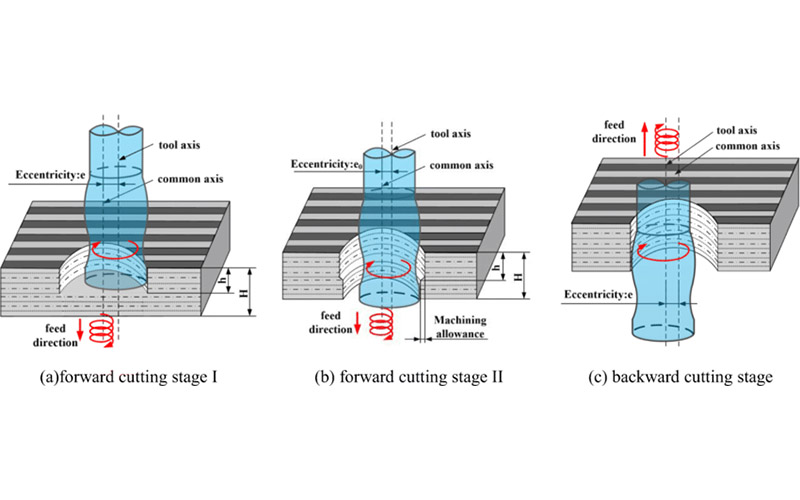
Conventional Milling
In conventional milling, the milling cutters rotate in the same direction as the spindle axis of the milling machine. The milling cutters cut into the surface of the workpiece, creating precisely shaped and cut parts. This method is typically used to produce simple-shaped parts and is common in industrial production.
Climb Milling
In this method, the milling cutters rotate in the opposite direction to the spindle axis of the milling machine. This method is usually used to machine complex-shaped parts and asymmetrical cuts.
Basic CNC Milling Process
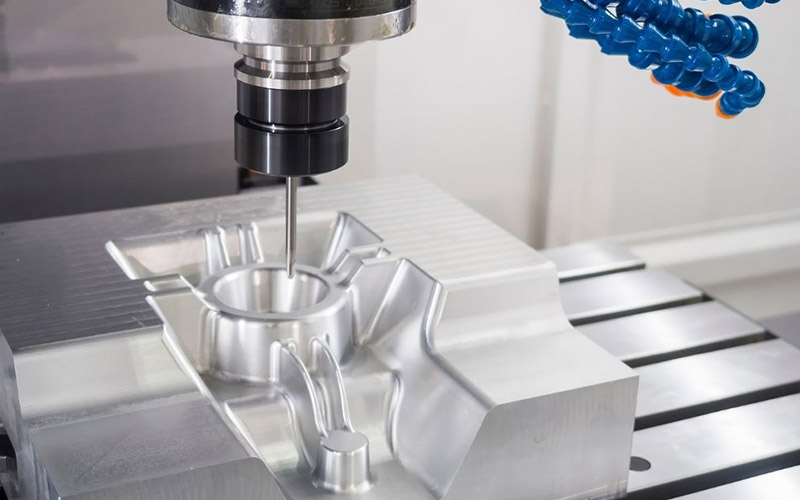
Check Workpiece and Material: First, the manufacturer will check the workpiece and material to ensure they meet technical and quality requirements. If necessary, the workpiece will be pre-machined before being placed in the milling machine.
Rough Milling: After checking and preparing the workpiece, the process begins with rough milling. Rough milling is the process of removing part of the material from the workpiece to create the precise shape and size of the part to be produced.
Design Data and Model Check on CAD: Before programming and machining, the design data and model are checked to ensure they meet technical requirements.
CAM Programming: The CNC milling machine is programmed using CAM software. This software translates the design files from CAD software into G-code, a series of precise commands for the CNC milling machine.
CNC Milling Machine Setup: Next, the technician sets up the CNC milling machine to ensure it operates correctly and meets machining requirements.
CNC Milling Operation: Finally, the CNC milling machine is operated to machine the part.
Materials for CNC Milling
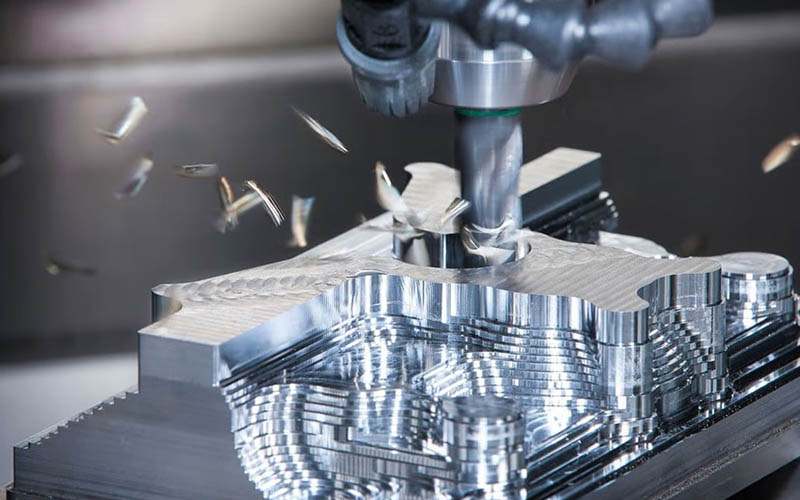
Here are some workpiece materials that can be used in CNC milling:
Material Name | Characteristics |
Aluminum 6061 | Lightweight, easy to machine, ductile, high-temperature resistant, corrosion-resistant, good strength |
Stainless Steel 304 | Corrosion-resistant, good hardness, high-temperature resistant, can be hardened by heating |
Brass C360 | Ductile, easy to machine, ductile, wear-resistant, good strength |
ABS | Durable, elastic, easy to shape, heat-resistant, corrosion-resistant |
Nylon (PA6 & PA66) | Elastic, high strength, wear and tear-resistant, high-temperature resistant |
POM (Delrin) | High strength, wear-resistant, heat-resistant, good elasticity, minimal shrinkage when temperature drops |
Applications of CNC Milling
CNC milling has many applications in various industries, including:
- Machinery Manufacturing: Using CNC milling to machine machine parts such as shafts, pulleys, gears, bearings, and other components.
- Automotive Industry: Producing car parts such as pistons, valves, engine bodies, wheels, steering parts, and other components.
- Aerospace and Maritime Industry: Manufacturing mechanical parts such as aircraft wings, wheels, steering systems, and other components.
- Electronics Industry: Producing parts such as circuits, sockets, frames, converters, and other components.
- Consumer Products Manufacturing: Producing products such as eyewear frames, watch parts, computers, pressure gauges, and other products.
- Medical Industry: Manufacturing parts such as support frames, bone replacement parts, shaping parts, and other components.
- Hand Tool Manufacturing: Producing products such as tools, knives, scissors, hammers, and other products.
- Jewelry Manufacturing: Producing products such as rings, necklaces, earrings, and other products.
- Electrical Equipment Manufacturing: Producing products such as controllers, sensors, sockets, and other products.
Where to Find CNC Milling Services in Ho Chi Minh City?
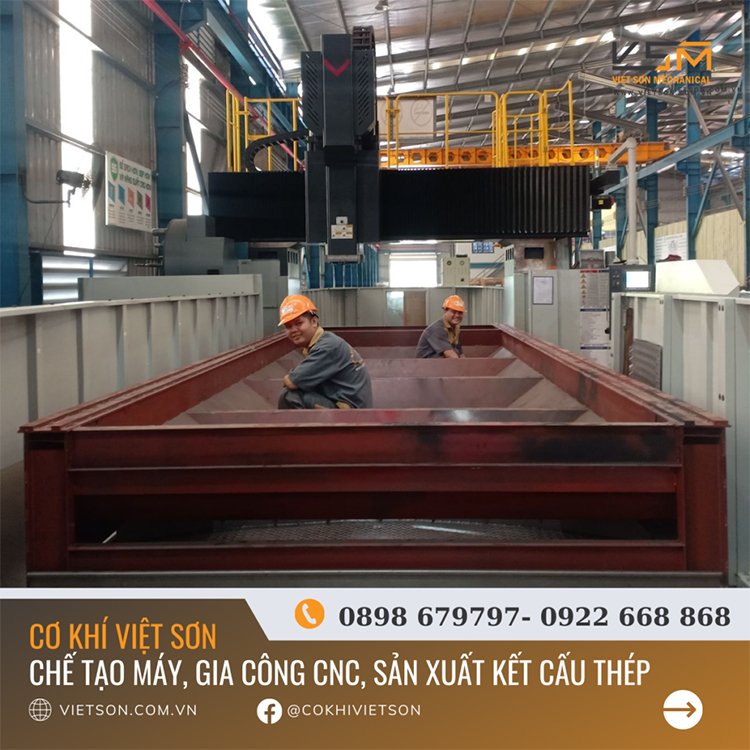
Viet Son Mechanical Co., Ltd specializes in manufacturing machine parts and milling products in Ho Chi Minh City, with many years of experience in mechanical manufacturing. Every mechanical product produced is of high quality. Viet Son Mechanical’s machining products are diverse, meeting the needs of even the most demanding customers, and we accept custom orders for detailed parts and precision machining.
With our experience and capabilities, we not only manufacture standard products and parts but also custom-make non-standard parts and various metal structures. Our equipment can machine products according to requirements and large metal parts such as machinery, metal shafts, large motors, etc.
If you need CNC milling services, contact Viet Son Mechanical Co., Ltd and we will answer all your questions.
Contact for Machining:
► Contact for Machining: 0922 668 868 (Zalo – Viber – WhatsApp)
► Address: Lot C2-7, Road N7, Tan Phu Trung Industrial Park, Tan Phu Trung Commune, Cu Chi District, Ho Chi Minh City
► Website: https://vietson.com.vn/
► Email: [email protected]
► Facebook: https://www.facebook.com/cokhivietson
► Youtube: https://www.youtube.com/channel/UC_n7V8NDRtO75pSOUOMiQ8w