A basic prefabricated house typically takes about 2 months to complete, significantly faster than traditional on-site construction. However, this does not mean that the essential steps are skipped. Planning, design, drawing creation, and selecting suitable materials still occur similar to other residential homes. Here are the necessary steps to construct a dream-like prefabricated house.
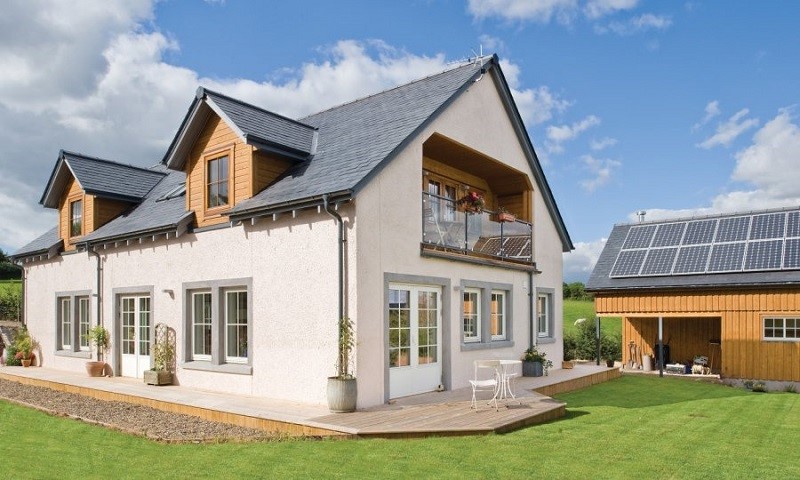
Understanding the steps in constructing a prefabricated house
Prefabricated houses, although simple and cost-effective alternatives, still follow a systematic and well-defined process. There are five basic steps involved:
Information exchange between the homeowner and the factory
During this stage, the architect and the buyer engage in discussions to understand the homeowner’s preferences, desires, and requirements for the future prefabricated house. As the experienced and technically knowledgeable party, the architect provides guidance and sketches a preliminary model of the ideal home. Simultaneously, the buyer expresses any necessary modifications and provides clearer insights into their intentions until both parties reach a mutual understanding.
Following the exchange, a temporary plan is established, encompassing details such as costs, materials, location, and completion timeframe. Naturally, this information is provided by the seller/contractor.
During this stage, the buyer can request references to previous projects undertaken by the company. While some details may be kept confidential, up to 80% of information, including design styles and estimated costs, is typically disclosed. This serves as a celebratory achievement for the construction company.
Finalizing 3D drawings and production
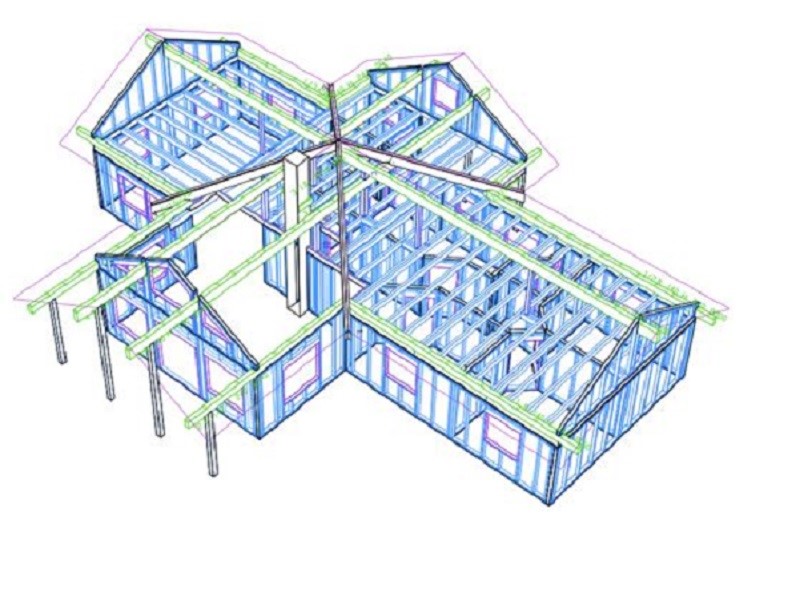
Once all the details are approved by the involved parties, particularly the buyer, the construction company proceeds to create the production drawings to calculate the completion intensity and analyze the aspects that will have an impact. This stage usually takes 3-4 weeks. Although it is a relatively long time, when the final drawings are completed, the buyer can immediately visualize whether the future house aligns with their initial vision. This process is carried out by skilled architects using specialized 3D modeling software for prefabricated houses, which allows for detailed rendering of the structure.
Production process
As soon as the production drawings are completed, the actual construction of the house begins. The first priority is always the selection of materials, which is handled by the procurement department of the factory. The quantity is determined by the manufacturing side, and the purchased materials are stored in dedicated warehouses.
The structures of the prefabricated house are calculated using computer technology with an accuracy of 1mm, ensuring high-quality standards. The production time depends on the scale of the project. For a standard 150m2 house, it usually takes about 3-4 weeks to complete the details within the factory. The finished structural components will be moved to a separate storage area to await transportation. The components are then transported to the assembly site using the company’s standard trucks.
Typically, the factory will send product photos and provide detailed updates on the progress to the buyer. The homeowners are allowed to visit the factory to closely monitor the construction process. However, they must comply with the regulations set by the manufacturer to ensure safety and progress.
Assembling the prefabricated house
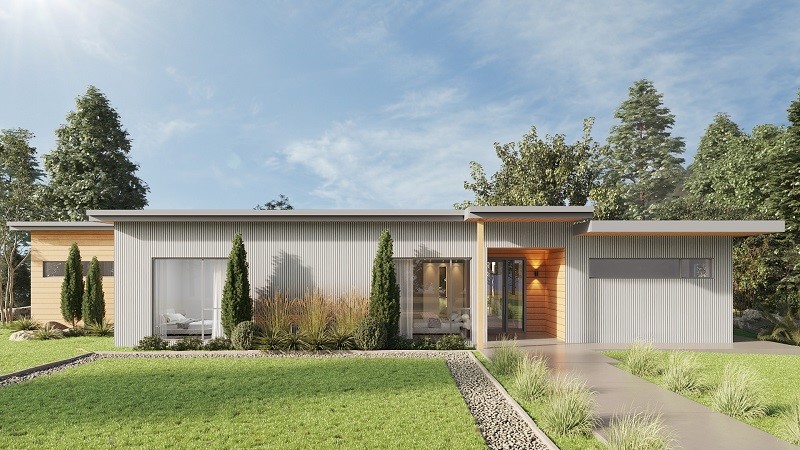
Typically, the structural components of the house are transported using containers, and upon arrival, cranes are used for installation. This process takes 5-7 days to complete. For larger-sized houses or those with high technical requirements, the timeframe may be longer.
A standard-sized prefabricated house usually requires the use of 2-3 trucks for transportation. In some cases, the manufacturing and assembly units come from different organizations. They can either be partners or contractors hired by the homeowners themselves.
Project Completion of Prefabricated House
The project is considered complete only when the customer is satisfied. Naturally, quality inspection is an essential step that cannot be overlooked. Most construction companies provide support and address any additional inquiries or concerns raised by the homeowners.
Some Notes to Consider When Hiring a Prefabricated House Contractor
A home is an invaluable asset for many people, and unfortunately, encountering an irresponsible or unskilled construction company can lead to a “loss of money and trouble” scenario. To avoid feelings of regret, you can refer to the following notes:
- Research websites or seek advice from experienced individuals. If your friends or family members have not purchased a prefabricated house before, you can explore specialized forums dedicated to discussing such matters. Here, you can find both experts and people who have previously experienced these services.
- Compare prices and services from multiple contractors to make an informed decision.
- Request to view previous projects completed by the contractor.
- Only collaborate with establishments that have clear processes and transparent contract terms. If possible, visit the factory before proceeding with the partnership.
Typically, contractors also handle the procurement of materials. Once you choose a reputable business, you don’t have to worry about this aspect. However, if you lack confidence, you can discuss the option of selecting an external material supplier with the contractor.
In conclusion, constructing a prefabricated house may involve additional steps such as obtaining building permits and confirming ownership, but ultimately, it still follows the five fundamental steps mentioned above. The remaining tasks will be addressed and supported by the contractor.