In the era of technology 4.0, CNC cutting has been a huge and indispensable part in the modern machine industry. With having machinery and numerical control technology combined, CNC cutting has revolutionized a lot of machining as well as manufacturing processes. CNC cutting can be applied to machining metal parts with precision as well as creating diverse and complex products. Let’s explore more about this amazing technology and all it has to offer.
What is CNC cutting?
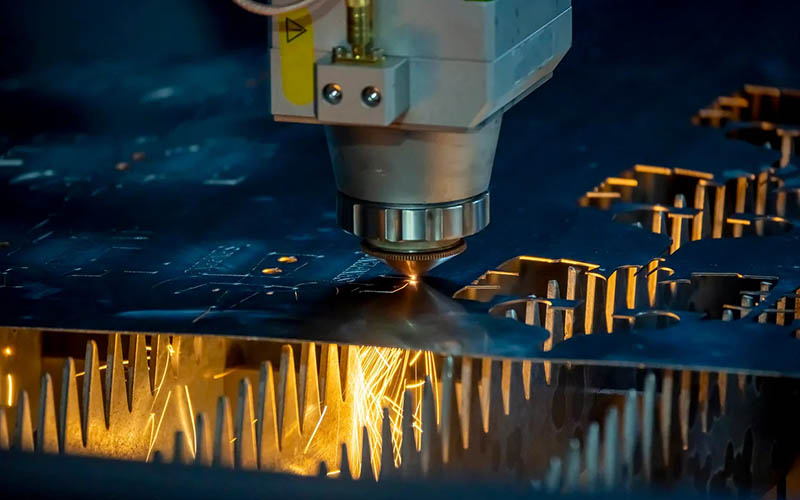
CNC cutting is a very precise cutting process using a CNC (Computer Numerical Control) lathe. CNC is an automated manufacturing technology that relies on precise control of motors and cutting tools made by computer commands.
During the process of CNC cutting, a model or a technical drawing of a part is entered into a CAD/CAM software, which converts the information into the control commands in the computer for the CNC lathe. The CNC lathes will use motors or cutting tools to cut out or machine the part that is required.
The process of CNC cutting is a very precise and accurate process and can be applied to a wide range of materials such as: metal, wood, plastic, and composite materials. It allows the production of the parts to be in high precision, high complexity, and a good repetition rate.
CNC cutting can be used in many industries such as precision mechanical industries, automotive industries, aerospace industries and much more.
What is CNC cutting machines? Structure of CNC cutting machines explained
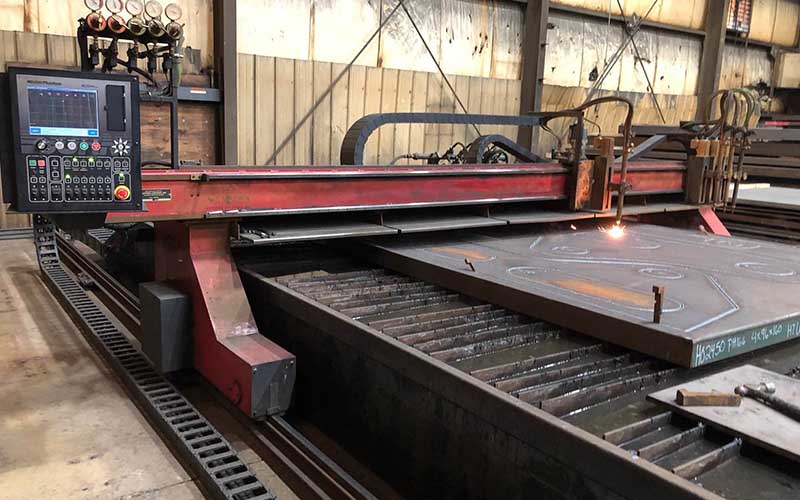
A CNC machine, also more commonly known as a CNC lathe or a CNC milling machine, is a type of computer operated machine tool that is used to cut, machining, and shape parts precisely and accordingly to its design plans. CNC cutting machines are used widely in many industries to produce complex parts and help meet exact product requirements.
The basic structure of a CNC cutting machine includes:
–Chassis: Acts as an outer frame to support other components on the inside and provides rigidity and stability for the cutting process.
-Working table: The working table is a flat surface on the machine used to hold and mount the work piece in place. The workbench can be moved in different directions to cut the part as required.
–Cutting Head: The cutting head is usually attached to the spindle of the machine and can be used as a cutter, milling cutter, drill bit or other cutting tools depending on the specifications of the application. The cutting head is operated by motors to help it cut and perform machining operations.
–Spindle: The spindle is the main rotating shaft on the machine and is where the cutting head is placed and rotated. It is operated by spindle motors and can move in different directions to cut and perform machining operations.
–Control system: The CNC cutting machine is controlled by a numerical control system (CNC) through computers and control software. This system converts the commands in the engineering drawing into control commands. This control system then makes commands for the cutter, manages the movements of the axes, and control the cutting and machining operations.
–Cooling system: Since the cutting process generates a lot of heat, most CNC cutting machines have a built-in cooling system to control the temperatures and makes sure that the machine does not overheat.
This is just the basic constructions of a CNC cutting machine, different components and functions can also be added to the machines depending on the types of applications and the intended use of the machine.
Working Principles of a CNC cutting machine
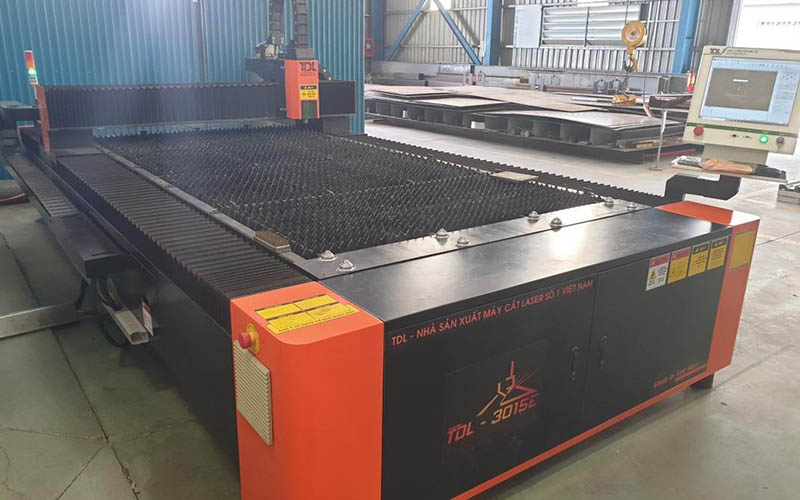
The way a CNC cutting machine operates is based on a combination of mechanical, electronic and computer components. Here is an overview of how the machine works:
–Design and programming: Before the process of machining, a model or technical drawing of the desired part to be machined must first be made using CAD (Computer-Aided Design) software. Afterwards, a CNC machining program is created using CAM (Computer-Aided Manufacturing) software. This program will convert the model into control commands for the CNC cutting machine.
–Preparing materials and machine: The material that is going to be machined will be prepared and placed on the worktable of the CNC machine. The suitable cutting tools will be placed on the cutting head of the machine.
–Machine control: Once the machining program has been loaded to the CNC control computer, the machining process will begin. The control computer will send out corresponding commands to the motors and other control systems on the cutting machine.
–Axis Movement: The CNC cutting machine controls the position and the movement of the axes of the cutting head to the correct position. The main axes, X, Y, and Z are controlled using motors and a screw system to move precisely and synchronously together.
–Cutting and machining: When the cutting head is positioned correctly on the machine, all cutting and machining operations will be performed according to the CNC machining program. The programmed cutting head moves and performs cutting, milling, drilling, grinding and other machining operations to create the desired shape of the model part made.
–Quality Control: CNC machines are equipped with a sensor system and gauges to check for the quality and accuracy of the part that is being made during the machining process.
Through all the above steps, the CNC cutting machine can perform precise cuts and machining according to the programmed design. This ensures accuracy, consistency, and high performance in the production of making and machining the complex and precise parts.
Advantages and Disadvantages of the CNC cutting machine
Advantages
–High Precision: The CNC cutting machine are capable of cutting and machining with high precision, even with complex parts. This ensures that the end result of the part is in the correct shape and size as designed on computer.
–Stability and Repeatability: CNC machines are capable of maintaining high stability as well as repeatability during machining and other usages. Once the machine has been properly set-up, the machine will perform the exact same cuts and machining every time with guaranteed precision and consistency.
–Increased Productivity: CNC cutting machines are fully automated and performs automatic cutting and machining operations, reducing reliance on manual labor. This helps increase productivity and production efficiency while reducing labor time and effort.
–Wide ranges of applications: CNC cutting machines can be used and operated on a variety of materials such as metal, wood, plastic, and composite materials. This opens up many application opportunities in many different industries such as mechanical, automotive, electronic, medical, furniture and many more different industries.
Disadvantages
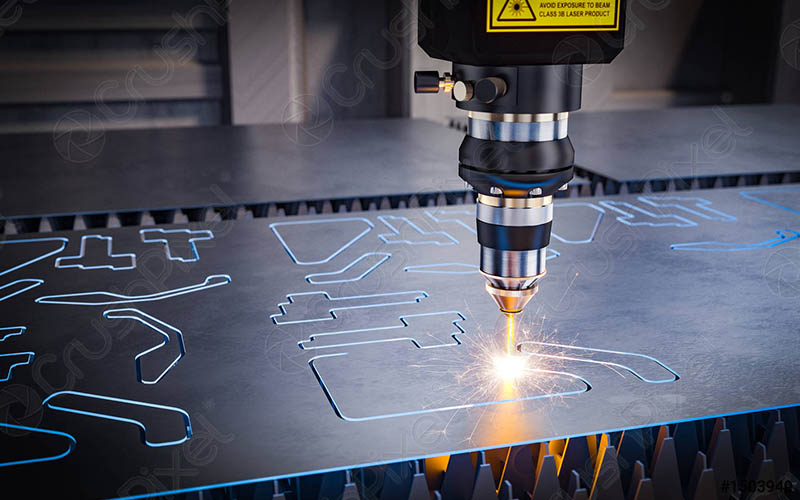
–Requiring technical knowledge: To be able to operate and program a CNC cutting machine requires a high amount of technical knowledge. People who use this machine needs to understand and master the mechanics, electronics, and the control software in order to use the machine effectively.
–Requires a high starting investment cost: CNC cutting machines have a much higher starting investment cost compared to other traditional cutting tools. This can be an issue especially with smaller businesses or individuals that are looking to adopt to CNC technology.
–Difficulty changing its dynamics: CNC cutting machines are only programmed to perform a specific job.
Types of CNC cutting technology
CNC cutting technology has many different methods for cutting and machining materials. Here are some common classifications of CNC cutting technology:
Laser Technology
–Laser technology uses a high-power laser to cut and process materials such as metal, wood, plastic, and non-metallic materials. Laser technology is capable of cutting materials accurately and quickly and is widely used in many industries.
Plasma cutting technology
–Plasma cutting technology uses a high-temperature plasma arc to cut ductile materials such as metal, stainless steel, and aluminum. Plasma cutting technology is most commonly used in industrial applications such as thick metal sheet cutting and construction work.
Waterjet cutting technology
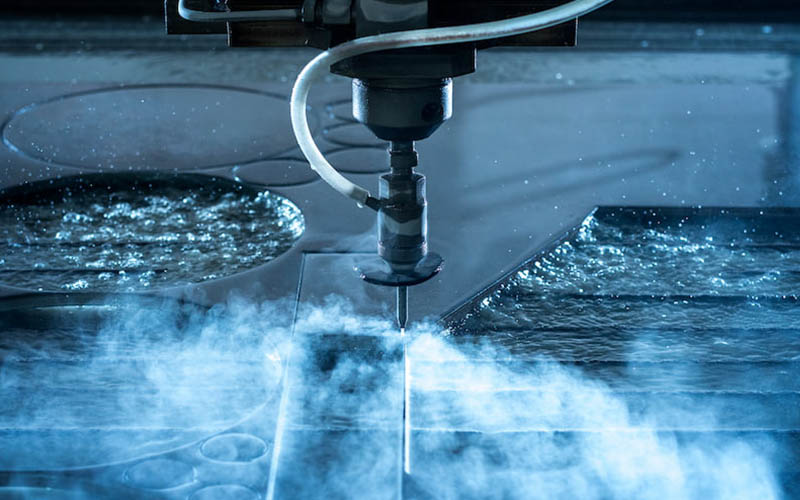
-Waterjet cutting technology uses a combination of high-pressured water with sand grains or just high-pressured water to cut and process materials. This technology is suitable for a wide range of materials from metal to wood, stone, brick, and plastic.
Spark wire cutting technology/EDM cutting technology
-EDM cutting technology uses a wire or electrode to generate a strong electrical pulse to cut and process ductile materials such as metals and alloys. EDM technology is often used to cut complex parts or difficult-to-cut materials.
Furthermore, other cutting technologies such as laser tube cutting, plasma tube cutting, wire EDM, oxygen gas cutting, and more are available depending on the specific requirements of the application. Each cutting technology has its own advantages and disadvantages and choosing the right technology all depends on factors such as: the material, thickness of the material, required accuracy and manufacturing process.
Applications of CNC cutting
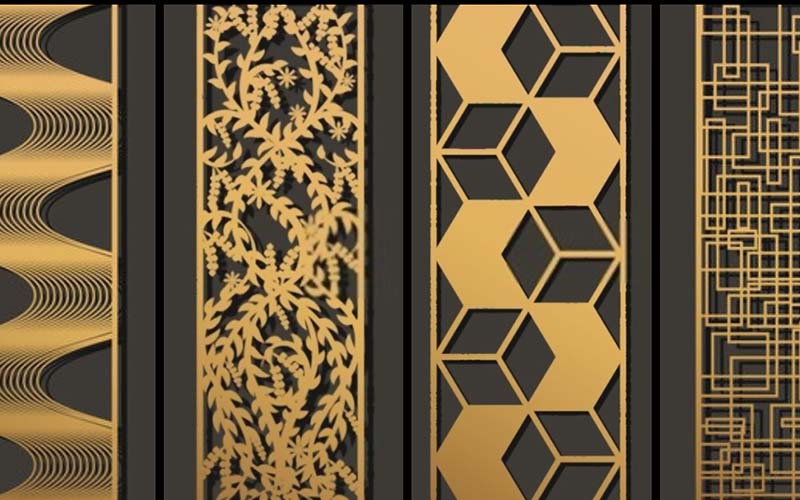
CNC cutting technology has many applications in different industries. Here are some examples of how CNC cutting is used in different industries:
–Mechanical industry: CNC cutting is widely used in the mechanical industry to machine metal parts such as sheet metal, pipes, shafts, and other materials. It can cut and process materials such as steel, aluminum, copper, stainless steel, and alloys.
–Automotive industry: CNC cutting is used for machining automotive parts such as chassis, bumpers, hinges, and other precision parts. It helps to create high-precision parts and reduce production time.
-Aviation and space industry: In the aeronautics and space industry, CNC cutting is used to make aircraft and spacecraft parts. CNC cutting helps to ensure accuracy and consistency when making theses critical parts and helps improve performance and safety.
-Electronic industry: CNC cutting is used in the electronics industry to machine parts such as printed circuits, electronic devices, electronic device enclosures, and other small parts in the electronics industry. This also helps to create precise and compact electronic products.
–Furniture industry: CNC cutting is used in the furniture industry to create wood, plastic, and composite furniture parts. CNC cutting machines helps speed up production of interior parts such as doors, tables, chairs, and wall panels.
-Advertising and media industry: CNC cutting is used to create signs, signboards, braille, and other media products. It helps allow precise cutting and creation of innovative designs.
Prestigious CNC metal machining unit
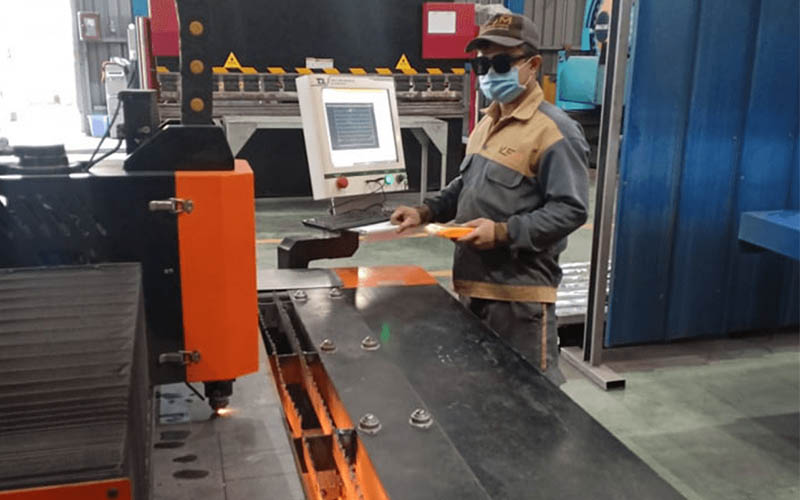
Viet Son Mechanics owns an advanced CNC machining technology as well as modern equipment. All staff and technicians at Viet Son Mechanical are highly trained and experienced in operating CNC cutting machines and handling complex metal working jobs.
Viet Son Mechanical is dedicated to providing high quality products and services and fully meeting requirements and standards of our customers. We place an emphasis on consistency, accuracy, and responsive delivery times.
In addition to CNC metal cutting, Viet Son Mechanical also provides other machining services such as turning, milling, grinding, and welding. This allows customers to enjoy a comprehensive service and meet diverse machining requirements.
With the prestige and quality of the products produced, Viet Son Mechanical is proud to be a reliable CNC metal machining unit, meeting the processing needs of customers in different industries.
CNC cutting technology has now become one of the most important and indispensable technologies in the modern machining industry. With its high consistency, high performing, precision cutting and machining capabilities, CNC cutting machines have brought great benefits to many industries. From machining complex parts to creating precise and diverse products, CNC cutting and greatly developed the competitiveness and production efficiency in many industries. With the continuous development of this technology, CNC cutting will continue to play an important role in the future and meet the increasing requirements of the market.